Compression springs or coil springs are mechanical energy accumulators that absorb forces when they are compressed and release the forces when they are released. Gutekunst Federn offers quick selection and procurement of compression springs in its catalog program on Federnshop.com 4536 different sizes in mild steel EN 10270-1 and stainless steel EN 10270-3-1.4310 directly from stock. And if no suitable compression spring is available in the store, Gutekunst Federn also manufactures any desired compression spring up to 12 mm wire thickness from a wide variety of spring steels in small quantities and large batches.
Table of Contents
Properties of compression springs
Compression springs are made from round, oval or square spring steel wires. Most of the spring steel wire is brought into any desired shape in the cold forming process, either by winding it around a mandrel or, in the case of fully automatic spring coiling machines, with the help of wire guide pins. The compression springs are usually made cylindrical and with a constant pitch. The manufacturing tolerances are defined from quality grade 1 (smallest tolerance) to quality grade 3 (greatest tolerance) according to DIN EN 15800. The calculation of the compression springs is based on the EN 13906-1 standard. The spring calculation was carried out with the Gutekunst spring calculation program WinFSB . A Collection of formulas for the calculation of compression springs Is there … here.
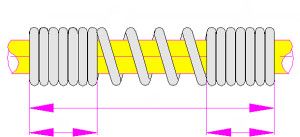
Structure of coils, spring designs and spring systems for compression springs
In addition to the classic compression springs with a constant pitch, the coil spacing can also vary in order to influence the spring characteristic. Windings are also often wound in the middle or at the spring ends in a block to prevent catching when handling the compression springs. In addition to cylindrical spring design , with an even spring characteristic , conical, double-conical or beehive springs with a variable spring characteristic and some advantages in terms of fatigue strength are also used very often. Different spring systems, such as series, parallel or mixed circuits, are also regularly used when it comes to distributing forces or variable spring characteristics.
Spring ends and spring end bearings in compression springs
After the compression springs have been coiled, tempering takes place in order to reduce the internal stresses in the spring and to increase the shear elastic limit. This reduces the amount of setting of the compression spring. The respective tempering temperatures and times depend on the material type; cooling takes place in air at room temperature. From a wire thickness of 0.5 mm, the spring ends are usually placed and ground in order to ensure a plane-parallel mounting of the spring and an optimal introduction of force. A grinding angle between 270 ° and 330 ° is ideal. Spring ends with wire diameters smaller than 0.5 mm are only laid out. In order to be able to guarantee the required spring properties, such as structural dimensions or force properties after manufacture, certain spring dimensions are tolerated as production compensation.
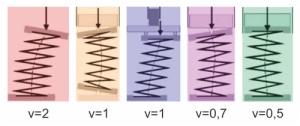
Compression springs tend to buckle the longer and thinner they are. To the kink limit To check / determine the respective compression spring, it depends on the spring end bearing. In the standard EN 13906-1, point 9.14, the different spring end bearings described. When guided by a mandrel or sleeve, the compression spring cannot buckle. However, the friction created by the guide influences the suspension behavior, which takes the form of a hysteresis loop maps. Part of the spring work is converted into heat and is therefore lost. In addition, a certain percentage of the spring force lost when the spring is compressed for a long period of time at higher temperatures. This loss of strength is called relaxation , and it increases with increasing temperature and voltage.
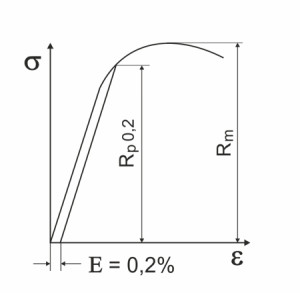
Shear stress and spring force in compression springs
In addition, when the compression spring is loaded, the shear stress the permissible value of the yield strength Rp, a permanent deformation occurs, which is expressed in the reduction of the unstressed length. This process is called “setting” in spring technology, which is associated with the terms “creeping” and “ relaxation “From materials engineering is to be equated. In order to counteract the setting behavior, the compression springs are coiled longer by the expected setting amount and later compressed to block length. This setting enables a better material utilization and allows a higher load in later use.
The spring force / spring stiffness depends on the spring steel wire and the spring rate or spring constant from. The spring rate also defines the ratio of spring force to spring travel. Basically, the dimensioning of the spring force can be influenced by the following measures.
- Wire diameter (d) greater = spring harder
- Coil diameter (De) greater = spring softer
- number of spring coils (n) greater = spring softer
Spring steel wire
The selection of the spring steel wire not only influences the spring force, but also offers the right material properties for the various spring applications. In addition to normal unalloyed spring steel wires, stainless spring steels are also used for stainless steel springs, e.g. in medical and food technology, SiCr-alloyed valve spring wires for fatigue strength applications, copper alloys for good electrical properties, nickel alloys for high heat and corrosion resistance, and titanium alloys for the highest demands from aerospace technology.
Offer compression springs
Gutekunst Federn offers compression springs in 4536 different sizes directly from stock or individually manufactured from the various spring steels up to 12 mm wire thickness in small quantities and large series. You can find the compression spring shop here . For an individual and non-binding pressure spring offer, please send the required spring data to service@federnshop.com or contact our quotation department directly at (+49) 07123 960-197.
Related Links: