Die richtige Metallfeder für den gewünschten Einsatzzweck auszuwählen ist nicht immer einfach. In vielen Fachbüchern mit konstruktiven Grundlagen wird das Thema Federn sehr allgemein abgehandelt.
Falls Sie auf der Suche nach einer Standardfeder sind, finden Sie in unserem Lagerprogramm ein umfangreiches Federnsortiment mit 12.600 Baugrößen in Normalstahl und Edelstahl. Wenn nicht, senden Sie die gewünschten Federnparameter zur Auslegung und Angebotserstellung über die Federnanfrage. Zur Übersicht, haben wir nachfolgend die wichtigsten Parameter zur Bestimmung der passenden Metallfeder zusammengestellt.
Zu Beginn eine kurze Übersicht zu den unterschiedlichen Federnarten:
Druckfedern
Druckfedern werden mit Abstand am häufigsten eingesetzt. Das liegt nicht nur an der Richtung der Krafteinwirkung, sondern vor allem an den besseren Belastungseigenschaften der Druckfeder. Denn Druckfedern können besser mit größeren Kräften und für Dauerfestigkeitsanwendungen mit Lastwechseln über 107 umgehen. Neben der großen Auswahl an Material für die unterschiedlichen Anwendungen kann bei der Druckfeder die Einsatzvielfalt mit verschiedensten Oberflächenbehandlungen problemlos erweitert werden. Aufgrund der Leistungsdaten der Druckfeder ist es in manchen Fällen sogar sinnvoller, eine Zugfederanwendung auf eine Druckfeder umzubauen.
Zugfedern
Zugfedern werden am zweithäufigsten eingesetzt. Überall dort, wo die Krafteinwirkung nicht auf Druck, sondern auf Zug erbracht werden muss, kommt man an der Zugfeder nicht vorbei. Insbesondere die spezielle Bauform mit den beidseitigen Ösen birgt einige Risiken, die bei der Zugfederauslegung berücksichtigt werden müssen. Auch, dass die Zugfeder bei einem Federbruch ihre Federkraft komplett verliert, sollte bei der Verwendung einer Zugfeder beachtet werden. Mit der Materialauswahl ist die Einsatzvielfalt der Zugfeder bereits größtenteils ausgeschöpft, da aufgrund der aneinander liegenden Windungen das Aufbringen einer Oberflächenbehandlung nur mit einem erhöhten Aufwand möglich ist.
Schenkelfedern
Schenkelfedern werden bei Drehbewegungen eingesetzt, also überall dort, wo eine Biegebeanspruchung auftritt. Bei den Schenkelfedern gibt es keine besonderen Bauformen, d. h. der Federkörper einer Schenkelfeder ist immer zylindrisch mit einer linearen Federkennlinie. Bei den Schenkelfedern kommt es eher auf die individuelle Schenkelform an, die optimal zur Krafteinleitung der Drehbewegung angeformt wird. Wie bei der Zugfeder ist es auch bei der Schenkelfeder durch die aneinander liegenden Windungen schwierig, weitere Eigenschaften durch eine nachträgliche Oberflächenbehandlung aufzubringen.
Table of Contents
Festlegung der Federkennlinie
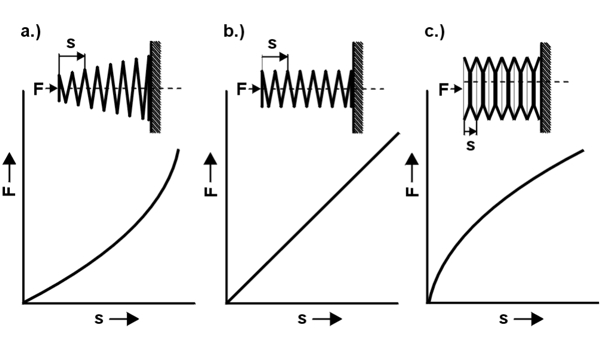
Grundsätzlich werden Metallfedern nach ihrer Kennlinie beurteilt. Die Federkennlinie ist der Charakter der Metallfedern. Diese stellt das Verhältnis der Federkraft „F“ zum Federweg „s“ dar. Je nach Federntyp, Federnbauform, Windungsabstand und Federsystem kann man lineare, progressive, degressive oder kombinierte Federkennlinien erzeugen. Bei einer linearen Federkennlinie (Bild b: zylindrische Feder) wird die Kraft gleichmäßig abgegeben, bei einer progressiven Kennlinie (Bild a: konische Feder) verstärkt sich die Kraftentfaltung mit Zunahme der Belastung und bei einer degressiven Kennlinie (Bild c: Tellerfeder) verringert sich die Kraftentfaltung mit der Belastung.
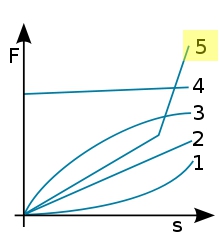
Bei der kombinierten Federkennlinie (Bild d: Kennlinie 5) werden unterschiedliche Kräftezustände entlang der Federkennlinie abgebildet. Diese kombinierte Federkennlinie kann mithilfe von Federsystemen erzeugt werden.
Anforderungen an die Metallfeder
Nachdem man sich mit der Federkennlinie bzw. dem Kraftverlauf auf den Charakter der Metallfeder festgelegt hat, müssen zur optimalen Auslegung der Metallfeder folgende Anforderungen abgeklärt und festgelegt werden:
- Belastungsart und Lebensdauer
- Statische oder quasistatische Belastung mit einer zeitlich konstanten (ruhenden) oder zeitlich veränderlichen Belastung mit weniger als 10.000 Lastwechseln insgesamt bzw. Hubspannung bis 0,1 x Dauerhubfestigkeit.
- Dynamische Belastung mit einer zeitlich veränderlichen Belastung mit mehr als 10.000 Lastwechseln insgesamt und Hubspannungen über 0,1 x Dauerhubfestigkeit. Dabei wird die Metallfeder meist vorgespannt eingebaut und einer periodischer Schwellbelastung mit sinusförmigen Verlauf ausgesetzt, die zufällig erfolgt, wie z. B. bei KFZ-Federungen. Dabei kann es auch zu schlagartigen Kräfteveränderungen kommen. Bei dynamischen Belastungen eignen sich vorwiegend Druckfedern und vereinzelt Zugfedern mit eingeschraubten Federenden.
- Einsatztemperatur
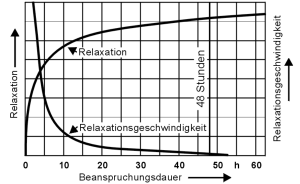
Die Einsatztemperatur beeinflusst entscheidend die Auswahl des passenden Werkstoffs. Aus diesem Grund gibt es bevorzugte Federstähle für Niedrigtemperatur- und für Hochtemperaturanwendungen. Besonders bei Hochtemperaturanwendungen muss die Relaxation des Federwerkstoffs bei der Kräfteauslegung berücksichtigt werden. Dabei tritt unter permanenter Spannung und höheren Temperaturen ein Kraftverlust auf, der mit steigender Temperatur und Belastungsdauer zunimmt.
- Umgebungsmedium
In welcher Umgebung wird die Metallfeder eingesetzt? Muss die Feder korrosionsbeständig sein oder gegen aggressive Säuren bestehen? Wird sie in der Lebensmittelbranche eingesetzt oder muss sie medizinisch rein sein? Alle diese Fragen beeinflussen die Auswahl des Federstahldrahts und einer möglichen abschließenden Oberflächenbehandlung.
- Benötigte Federkräfte und Federwege
Welche Federkräfte soll die Metallfeder bei bestimmten Federwegen erzeugen? Meistens werden die Federn vorgespannt eingebaut, d. h. die Feder erzeugt bereits eine bestimmte Vorspannkraft im Ruhezustand. Diese Kraft wird als „F1“ vorgespannte Federkraft beschrieben. Dazu muss die benötigte Federkraft benannt werden, welche die Feder im gespannten Zustand erreichen soll. Diese Federkraft wird als „F2“ gespannte Federkraft beschrieben. Zu diesen beiden Federkräften müssen noch die jeweiligen Federwege „s1“ und „s2“ oder Federlängen „L1“ und „L2“ bestimmt werden. Besonders bei dynamischen Belastungen kommt es auf den Federhub „sh“ an, der den Federweg zwischen „s1“ und „s2“, bzw. zwischen „L1“ und „L2“ beschreibt. Je kleiner der Federhub ist, umso besser ist die dynamische Belastbarkeit der Metallfeder.
- Vorhandener Einbauraum
Welche Dimensionen hat der Einbauraum, in der die Feder eingesetzt werden soll? Welchen Durchmesser und welche Länge darf bzw. muss die Metallfeder besitzen, damit sie eingebaut werden kann? Diese Baumaße sind Voraussetzung für die Auslegung der passenden Federn. Dabei müssen auch die Toleranzwerte der jeweiligen Maße im ruhenden und belasteten Zustand berücksichtigt werden.
- Einbausituation
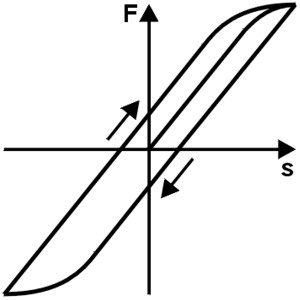
Dazu muss, je nach Druck-, Zug- oder Schenkelfeder, die Einbausituation überprüft werden. Wird z. B. die Druckfeder durch einen Dorn oder innerhalb einer Hülse geführt, muss die Reibung während der Federarbeit in einer Hystereseschleife berücksichtigt werden. Wird die Druckfeder ohne Führung eingebaut, müssen die unterschiedlichen Knickgrenzen für die verschiedenen Federendlagerungen berücksichtigt werden. Bei Zugfedern ist dagegen wichtig, an welcher Position die Ösen eingehängt werden. So ist die optimale Krafteinwirkung bei Zugfedern zentrisch an beiden Ösen entlang der Federlängsachse. Sehr häufig werden Ösen auch seitlich ausgelegt. Das muss entsprechend bei der Federauslegung berücksichtigt werden. Und bei der Schenkelfeder müssen die Schenkelform und die Windungsrichtung der Einbausituation angepasst werden. Zudem ist es bei Schenkelfedern wichtig, dass diese immer nur in Windungsrichtung belastet werden.
- Toleranzfeld
Abschließend ist das Toleranzfeld der jeweiligen Federnart zu berücksichtigen. Denn jede Metallfeder wird bei der Produktion innerhalb eines bestimmten Toleranzfeldes gefertigt, sodass die Feder optimal für den Einsatzfall hergestellt wird. Dieses Toleranzfeld wird bei Metallfedern in Gütegrad 1, 2 und 3 ausgewiesen. Normalerweise werden Metallfedern in Gütegrad 2 gefertigt, was vor allem bei kleineren Federabmessungen einem Toleranzfeld von bis zu zehn Prozent entspricht. Bei Gütegrad 1, mit höheren Herstellungskosten, ist das Toleranzfeld am kleinsten und bei Gütegrad 3, mit geringeren Herstellungskosten, am größten.
Videos
Die wichtigsten Federparameter im Überblick
Zusammenfassend noch einmal alle wichtigen Federparameter für eine optimale Federnauswahl und Federnauslegung der Metallfeder:
Federnart
► Druckfeder · Zugfeder · Schenkelfeder · Federsystem
Federkennlinie
► linear · progressiv · degressiv · kombiniert
Belastungsart und Lebensdauer
Lebensdauer
► Lastwechsel (Federhübe) gesamt
Einsatztemperatur
► Umgebungstemperatur in der die Feder eingesetzt wird
Umgebungsmedium
► Flüssigkeiten, Gase … in der die Feder eingesetzt wird
Federkräfte bei bestimmten Federwegen bzw. Federlängen
► vorgespannte Federkraft = F1 bei s1 oder L1
► gespannte Federkraft = F2 bei s2 oder L2
F1 vorgespannte Federkraft in N
s1 Federweg vorgespannt oder L1 Federlänge vorgespannt
F2 gespannte Federkraft in N
s2 Federweg gespannt oder L2 Federlänge gespannt
Vorhandener Einbauraum
► Länge und Breite des Einbauraums
► Länge Feder zwischen Krafteinleitungspunkten
Einbausituation
bei Druckfedern
► Führung durch Dorn und/oder Hülse
► ohne Führung die Knickgrenze der Federendlagerung beachten
bei Zugfedern
► Krafteinwirkung zentral oder dezentral
► Ösenstellung (Verdrehwinkel der Ösen zueinander) und Ösenposition (zentrisch/seitlich)
bei Schenkelfedern
► Schenkelform zur optimalen Kraftaufnahme
► Windungsrichtung der Belastung
Metallfedern mit einer linearen Federkennlinie, in den Federwerkstoffen Normalstahl EN 10270-1 und rostfrei EN 10270-3-1.4310, findet man in 12.600 Federbaugrössen im Gutekunst Federnkatalog. Bei allen nicht linearen Federanwendungen senden Sie bitte die benötigten Federparameter einfach an verkauf@gutekunst-co.com oder nutzen Sie das Gutekunst Anfrageformular.
Weiterführende Links: