Selecting the right metal spring for the desired application is not always easy. In many technical books with constructional basics, the subject of springs is treated in a very general way.
If you are looking for a standard spring, you will find an extensive range of springs in our stock programme with 12,600 sizes in mild steel and stainless steel. If not, send the desired spring parameters for design and quotation via the spring enquiry. For clarity, we have compiled the most important parameters for determining the suitable metal spring below:
Compression springs
Compression springs are by far the most commonly used. This is not only due to the direction of the force application, but mainly due to the better load characteristics of the compression spring. This is because compression springs are better able to handle larger forces and, for fatigue applications, load changes in excess of 107. In addition to the large selection of materials for the various applications, the variety of uses for the compression spring can be easily extended with a wide range of surface treatments. Due to the performance data of the compression spring, it may even make more sense in some cases to convert a tension spring application to a compression spring.
Tension springs
Tension springs are the second most commonly used. Wherever the force has to be applied by tension rather than compression, there is no getting around the tension spring. In particular, the special design with the eyelets on both sides involves some risks that must be taken into account in the tension spring design. Also, the fact that the tension spring completely loses its spring force in the event of a spring fracture should be taken into account when using a tension spring. With the choice of material, the range of applications of the tension spring is already largely exhausted, since the application of a surface treatment is only possible with increased effort due to the adjacent coils.
Schenkelfedern
Torsion springs are used for rotary movements, i.e. wherever bending stress occurs. There are no special designs for torsion springs, i.e. the spring body of a torsion spring is always cylindrical with a linear spring characteristic. Bei den Schenkelfedern kommt es eher auf die individuelle Schenkelform an, die optimal zur Krafteinleitung der Drehbewegung angeformt wird. As with the extension spring, it is also difficult to apply further properties to the torsion spring by means of a subsequent surface treatment due to the coils lying next to each other.
Table of Contents
Determination of the spring characteristic
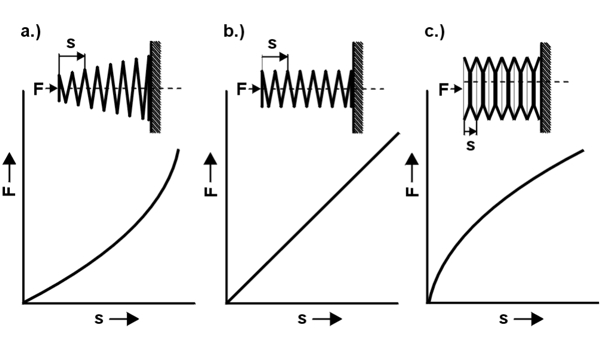
Basically, metal springs are judged according to their characteristic curve. The spring characteristic is the character of the metal springs. This represents the ratio of the spring force “F” to the spring travel “s”. Depending on the spring type, spring design, coil spacing and spring system, linear, progressive, degressive or combined spring characteristics can be generated. In the case of a linear spring characteristic (Fig. b: cylindrical spring), the force is delivered evenly, in the case of a progressive characteristic (Fig. a: conical spring), the force development increases with the increase in load, and in the case of a degressive characteristic (Fig. c: disc spring), the force development decreases with the load.
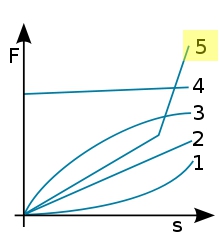
In the case of the combined spring characteristic curve (Fig. d: characteristic curve 5), different force states are mapped along the spring characteristic curve. This combined spring characteristic can be generated with the help of spring systems.
Requirements for the metal spring
Once the character of the metal spring has been determined with the spring characteristic curve or the force curve, the following requirements must be clarified and specified for the optimum design of the metal spring:
- Type of load and service life
- Static or quasi-static load with a time-constant (static) or time-varying load with less than 10,000 load cycles in total or stroke stress up to 0.1 x continuous stroke strength.
- Dynamic loading with a time-varying load with more than 10,000 load cycles in total and stroke stresses exceeding 0.1 x continuous stroke strength. In this process, the metal spring is usually installed preloaded and subjected to a periodic swell load with a sinusoidal curve, which occurs randomly, as in the case of car suspensions, for example. This can also lead to abrupt changes in forces. For dynamic loads, mainly compression springs and occasionally tension springs with screwed-in spring ends are suitable.
- Operating temperature
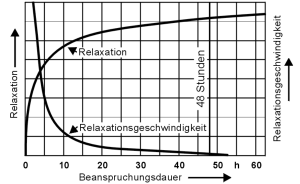
The operating temperature has a decisive influence on the selection of the appropriate material. For this reason, there are preferred spring steels for low temperature and for high temperature applications. Especially for high temperature applications, the relaxation of the spring material must be taken into account in the force design. A loss of force occurs under permanent tension and higher temperatures, which increases with rising temperature and duration of load.
- Ambient medium
In what environment is the metal spring used? Does the spring have to be corrosion resistant or resistant to aggressive acids? Is it used in the food industry or does it have to be medically pure? All these issues influence the selection of the spring steel wire and a possible final surface treatment.
- Required spring forces and spring deflections
What spring forces should the metal spring produce at certain spring deflections? In most cases, the springs are installed preloaded, i.e. the spring already generates a certain preload force at rest. This force is described as “F1” preloaded spring force. For this purpose, the required spring force must be specified, which the spring is to achieve in the tensioned state. This spring force is described as “F2” tensioned spring force. In addition to these two spring forces, the respective spring deflections “s1” and “s2” or spring lengths “L1” and “L2” must be determined. Especially with dynamic loads, the spring stroke “sh” is important, which describes the spring travel between “s1” and “s2”, or between “L1” and “L2”. The smaller the spring stroke, the better the dynamic load capacity of the metal spring.
- Available installation space
What are the dimensions of the installation space in which the spring is to be used? What diameter and what length may or must the metal spring have so that it can be installed? These dimensions are a prerequisite for the design of the appropriate springs. The tolerance values of the respective dimensions in the resting and loaded condition must also be taken into account.
- Installation situation
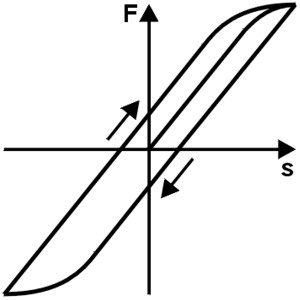
For this purpose, the installation situation must be checked, depending on the compression, tension or torsion spring. If, for example, the compression spring is guided by a mandrel or inside a sleeve, the friction during the spring work must be taken into account in a hysteresis loop. If the compression spring is installed without a guide, the different buckling limits for the various spring end bearings must be taken into account. With extension springs, on the other hand, the position at which the eyelets are hooked in is important. Thus, the optimum force application for extension springs is centric on both eyes along the longitudinal axis of the spring. Very often eyelets are also laid out on the side. This must be taken into account accordingly in the spring design. And for the leg spring, the leg shape and the winding direction must be adapted to the installation situation. In addition, it is important with torsion springs that they are only ever loaded in the direction of coiling.
- Tolerance field
Finally, the tolerance zone of the respective spring type must be taken into account. This is because every metal spring is manufactured within a certain tolerance range during production, so that the spring is optimally manufactured for the application. This tolerance zone is shown for metal springs in grades 1, 2 and 3. Normally, metal springs are manufactured in quality grade 2, which corresponds to a tolerance field of up to ten percent, especially for smaller spring dimensions. For grade 1, with higher manufacturing costs, the tolerance zone is smallest and for grade 3, with lower manufacturing costs, the tolerance zone is largest.
Videos
The most important spring parameters at a glance
In summary, all important spring parameters for an optimal spring selection and spring design of the metal spring:
Spring type
► Compression spring – Tension spring – Torsion spring – Spring system
Spring characteristic
► linear – progressive – degressive – combined
Type of load and service life
Lifetime
► Total load change (spring strokes)
Operating temperature
► Ambient temperature in which the spring is used
Ambient medium
► Liquids, gases … in which the spring is inserted
Spring forces for certain spring deflections or spring lengths
► Preloaded spring force = F1 at s1 or L1
► tensioned spring force = F2 at s2 or L2
F1 preloaded spring force in N
s1 Spring travel preloaded or L1 Spring length preloaded
F2 tensioned spring force in N
s2 Spring travel cocked or L2 Spring length cocked
Available installation space
► Length and width of the installation space
► Length of spring between force application points
Installation situation
for compression springs
► Guidance by mandrel and/or sleeve
► without guide observe the buckling limit of the spring end bearing
for extension springs
► Force application centralized or decentralized
► Eyelet position (twisting angle of the eyelets to each other) and eyelet position (centric/lateral)
for torsion springs
► Leg shape for optimum force absorption
► Winding direction of the load
Metal springs with a linear spring characteristic, in the spring materials normal steel EN 10270-1 and stainless steel EN 10270-3-1.4310, can be found in 12,600 spring sizes in the Gutekunst spring catalogue. For all non-linear spring applications, please simply send the required spring parameters to order@gutekunst-co.com or use the Gutekunst enquiry form.
Related Links: